Latest News
Specification Sales Manager
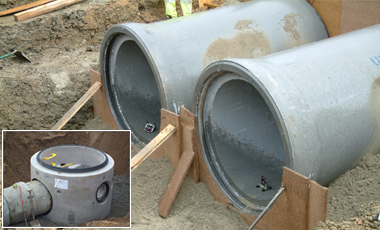
Salary up to £45k, plus car allowance, national role, Midlands Head Office
The Concrete Pipeline Systems Association (CPSA) is building on a period of industry growth and is now recruiting a specification sales Manager.
The main function of the role is to promote the specification and use of concrete pipeline systems to all relevant stakeholders including water utility clients and their alliance partners, public sector agencies and authorities, developers, design engineers, specifiers, and installers.
The successful individual will require an in-depth technical understanding of drainage and is likely to be a degree qualified civil engineer with a track record of success in specification sales within the sewerage sector or a closely related field.
The ideal candidate would also have a network of relevant industry contacts and is able to hit the ground running.
If you think this describes you and you want to join a nimble, forward-thinking trade association, please forward your CV and a covering letter, including details of your current salary, explaining why you think you are right for this role to:
Stuart.crisp@britishprecast.org
or
Mr Stuart Crisp
Business Development Director
Concrete Pipeline Systems Association
c/o The British Precast Concrete Federation Ltd
The Old Rectory
Main Street
Glenfield
Leicestershire
LE3 8DG
More news on pipeline bedding design
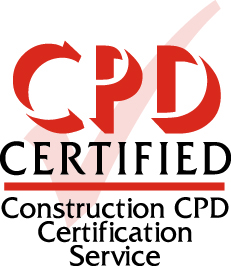
If our Blog in March and eBlast in May plus social media postings escaped your attention and you haven’t seen our ads and editorial coverage running continuously in the trade press since March, here’s another chance for you to reduce your pipeline installation costs and embodied carbon.
CPSA has produced a new CPD seminar “Optimising Pipeline Bedding Design to Achieve Installed Cost & Carbon Efficiencies”. The presentation brings CPSA’s total to four seminars independently accredited by the Construction CPD Certification Service and The Chartered Institution of Water and Environmental Management (CIWEM).
This new seminar demonstrates that substantial savings in pipeline installation costs and embodied carbon can be achieved through the effective use of structural design and the resulting selection of an appropriate pipeline embedment detail relevant to the pipe material and strength.
The seminar aims to provide the delegate with an awareness of the structural design fundamentals for buried pipelines and the main industry reference sources available. The presentation should lead to an appreciation of the importance of combining structural integrity with minimum installation costs and lower embodied carbon and how this can be achieved through an understanding and effective use of structural design.
To arrange a free CPD seminar, please visit https://www.precastdrainage.co.uk/page/cpsa-accredited-cpd-programme
How to make your product’s carbon footprint look good
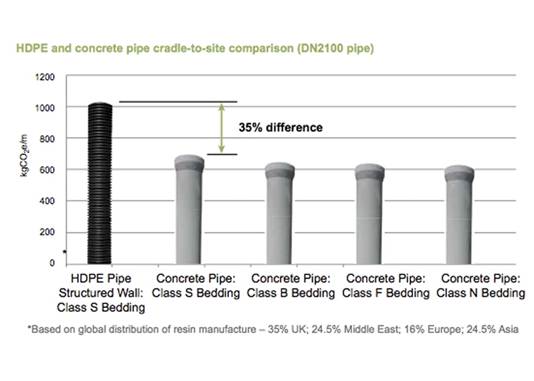
Will there ever be an end to the relentless series of claims by product manufacturers that their product has superior carbon footprint credentials compared with competitors’, only to be followed by those same competitors claiming superiority based on yet another set of studies?
And how do specifiers decide who to believe?
By way of an example, the concrete pipeline industry is fighting its own battle with plastic. In 2010 CPSA published a detailed report based on the most comprehensive study of its type ever undertaken, providing embodied carbon footprints for precast concrete pipes, manhole rings and cover slabs. This study was then used to produce two further reports providing carbon footprint comparisons between concrete pipes and plastic pipes and between alternative manhole construction methods.
The pipe comparison study indicates that concrete pipes have up to 35% lower cradle-to-site embodied carbon when compared with HDPE pipe using the same full granular (Class S) bedding design. However, rigid concrete pipes can often be used with alternative bedding designs using less imported granular material, whereas standard stiffness plastic pipes will invariably require Class S. The result of which is that the potential carbon (and installed cost) saving with concrete pipes can be even higher.
After several years silence, the plastic pipe industry responded. Using the embodied carbon values for concrete pipes from the CPSA study, an alternative set of values were presented for plastic pipes. These values were based on a much older “generic” study using Bath University’s Inventory of Carbon and Energy, taking an average across a wide spectrum of products and geographical sources; unlike the CPSA study for precast concrete pipes, there was no new study based specifically on the manufacturer’s own plastic pipe products. And the comparison did not include impacts for alternative bedding designs.
Using this generic data, the results of the study indicated a lower carbon footprint for plastic pipes.
But is this riposte valid? Is it right to use data specific to a single product type (CPSA concrete pipe study) and compare it with generic data across a wide spectrum that does not represent the manufacturer’s own product? Different accounting methods will lead to different results. Does it make sense to make a comparison where the results were derived by separate methodologies with different rules and boundary conditions?
Almost all UK carbon databases and calculators use data for plastic pipes that trail back to data for resins from a study in 2005 by TNO for Plastics Europe. Recently, the integrity of this data has been questioned as the allocations to distillate products used in the Plastics Europe study do not appear to comply with the rules set out in the construction industry’s most recognised methodology, EN 15804. The Plastics Europe study assumes that the plastic pipe manufacturer is located 100km from the source of the resin. For a UK plastic pipe manufacturer, this is extremely unlikely. Resin supplied from further afield, such as the Middle East and Asia will significantly increase the carbon footprint of plastic pipes manufactured in the UK due to higher emissions from grid electricity plus emissions associated with transport.
Be aware. The plastic pipe industry has not embraced EN15804, the main Standard for carbon accounting in Europe for construction products. Instead, they have elected to follow an alternative route via Product Environmental Footprints (PEFs). Maybe the numbers work out more favourable for plastic using PEF rather than EN15804?
Concrete pipes Vs Plastic Pipes. Which has the lower carbon footprint? Whose claims do you believe?
Digging deeper into carbon management
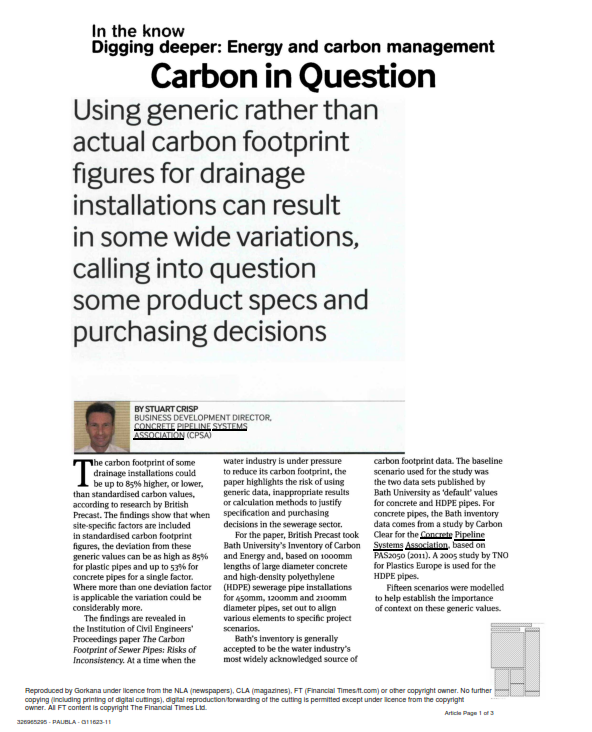
Faversham House has published an article in Water & Wastewater Treatment, based on British Precast's ICE Proceedings Paper “The 'carbon footprint' of sewer pipes: risks of inconsistency”
The sewerage industry needs to understand and reduce embodied carbon dioxide emissions associated with its assets in order to contribute to the national carbon dioxide reduction agenda. There are at least six recognised methodologies for calculating so-called 'carbon footprints' of construction products and tens of standard-based or ad-hoc calculators. With the increase in information from different sources, the use of different methodologies and the absence of representative data and data collection methods, there is a risk that inappropriate data, results or methods are used to justify crucial design, specification and procurement decisions in the sewerage sector. The ICE Proceedings Paper and article present an assessment of the problem and its impact on the reliability of embodied carbon dioxide emissions data for large diameter sewer pipes.
CPD Presentation Embodied Carbon Emissions in Concrete and other Pipeline Materials
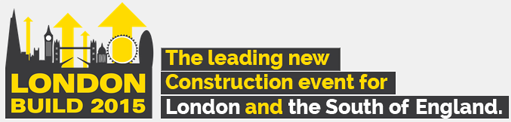
CPSA is delivering the CPD presentation Embodied Carbon Emissions in Concrete and other Pipeline Materials at LondonBuild 2015 at The O2 on Friday 19th June at the Building Solutions Workshop at 12.00 midday