Latest News
Marshalls Civils & Drainage gets straight to the Point on pollution
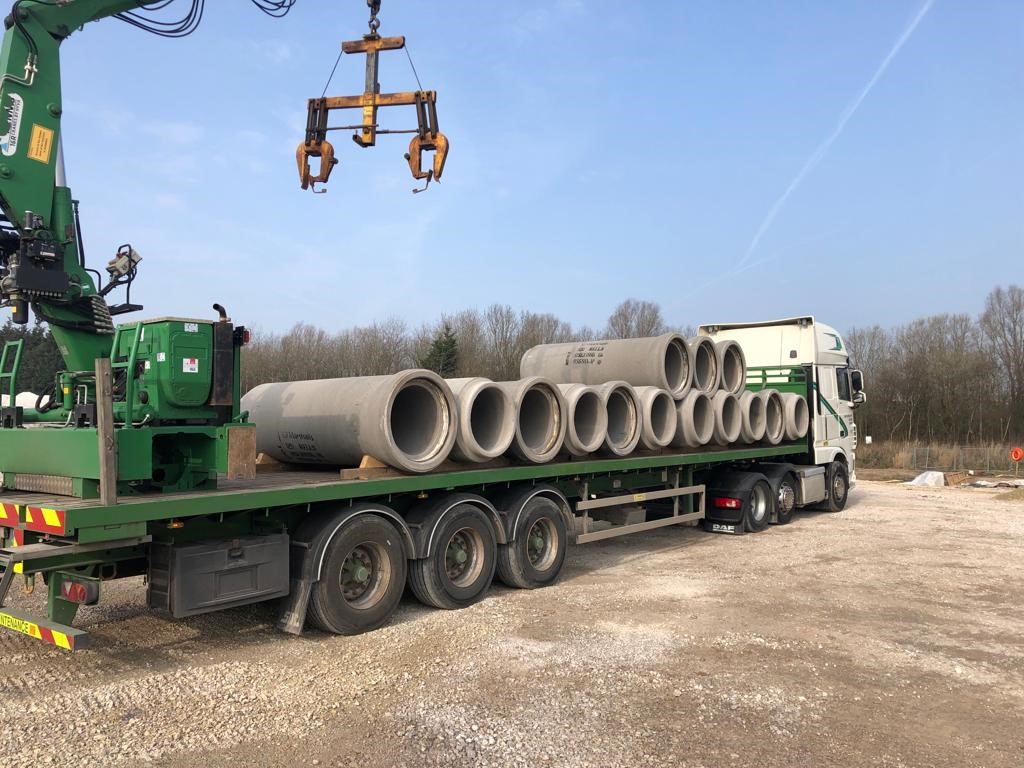
Pollution-resistant pipes from Marshalls Civils & Drainage help out at Gorsey Point.
Work is drawing to a close on a significant regeneration scheme in which bespoke concrete nitrile-seal drainage pipes by Marshalls Civils & Drainage have helped to mitigate potential contamination by pollutants.
Marshalls Civils & Drainage has supplied more than 140 precast concrete nitrile-seal pipes totaling 362m and in sizes ranging from 375mm to 675mm diameter to developer Marshall CDP’s Gorsey Point development in Widnes, Cheshire.
Gorsey Point is a new commercial development located on Gorsey Lane, approximately one mile from Widnes town centre. The 16-hectare site is located within the Widnes Waterfront area, a significant regeneration scheme that is transforming 145 hectares of low-quality industrial land into new commercial, residential and leisure facilities on the banks of the River Mersey, close to the new Mersey Gateway Bridge.
The former manufacturing site has been cleared to provide ‘oven-ready’ development opportunities and Marshall Construction is now constructing a three-phase development of warehousing and offices totalling approximately 700,000ft2 of space.
The site’s former industrial role has resulted in a legacy of contamination and, despite thorough remediation of the site, care still needs taking to ensure that any residual pollutants remaining underground do not leach out into the environment.
In particular, potentially aggressive petrochemical residues need preventing from compromising the site drainage system and entering local watercourses. Because of the need to protect against potential pollutants, Marshall CDP specified the use of precast concrete drainage pipes fitted with seals manufactured with nitrile rubber which is notable for being highly resistant to oil fuel and other chemicals.
The seals were manufactured for Marshalls Civils & Drainage by a specialist company in the Netherlands. Because they are specified infrequently, Marshalls Civils & Drainage offers them as a bespoke service which requires extended lead times to allow them to be produced, shipped to the UK and incorporated into the pipe manufacturing process.
Close liaison with the supply chain was therefore essential to ensure the 14-week lead time cause no disruption to the build programme. Efficient teamwork allowed site activities to be rescheduled to accommodate this without causing any delay.
In addition to the pipes, approximately 50 related pipe components, such as nitrile rockers, spigot and socket pipes for each pipe size were also supplied.
Marshall Construction’s project manager Tom Slattery said: “The pipes had to be nitrile sealed because of the contamination on the brownfield site. Everything went swimmingly – the pipes were no different to installing ordinary pipes, the only consideration was the long lead-time. “
“We were fully aware of this from the beginning and were able to make allowances in the build programme. Marshalls kept us fully informed at all times and by working closely with our supply chain we were able to plan and execute the installation smoothly and without any hiccups.”
For more information on concrete pipes please visit www.marshalls.co.uk/commercial/product/concrete-pipes
FP McCann go ultra-low carbon with Earth Friendly Concrete pipes and manholes
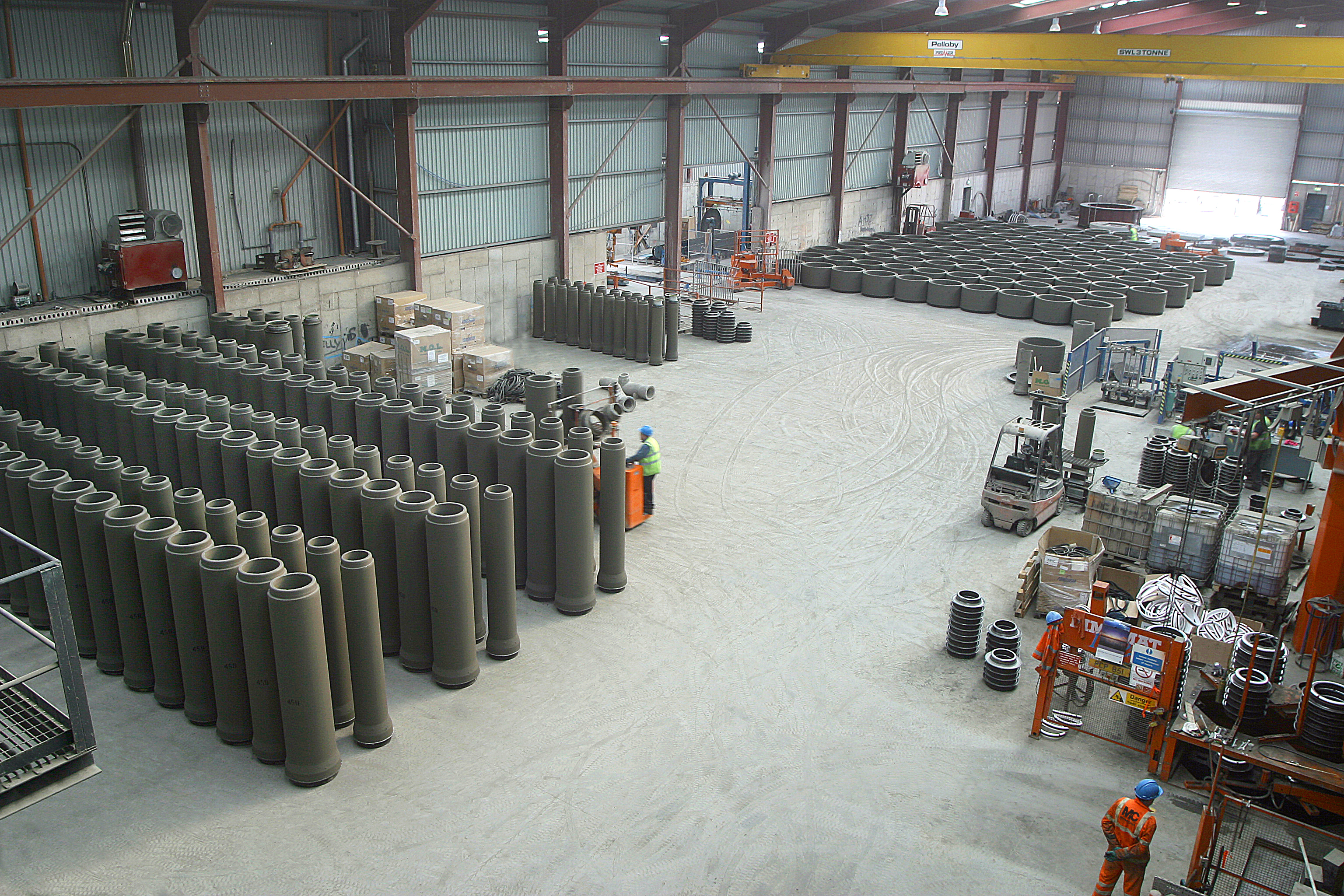
FP McCann trial of cement-free ultra-low carbon technology from Wagners marks the start of a new age for precast drainage in the UK
FP McCann has manufactured the UK’s first cement-free precast manhole rings and pipes at the company’s Knockloughrim precast factory using Wagners’ Earth Friendly Concrete (EFC) geopolymer concrete.
Portland cement usually makes around 70% to 80% of the carbon footprint of concrete. Wagner’s EFC employs a combination of chemical activators and low-carbon secondary cements, such as fly ash and Ground Granulated Blast-furnace Slag (GGBS), to replace Portland cement in the concrete mix, leading to significant reductions in the carbon footprint of concrete.
FP McCann worked closely with international partners, suppliers and customers to introduce the geopolymer low-carbon binder. Mass production trials at their concrete pipe factory in Knockloughrim, Northern Ireland, proved to be a success. In addition to its low carbon credentials, high performance concrete made with this novel material is achieving similar strengths to traditional concrete while, due to the chemistry of the geopolymer binder, providing improved durability in many aggressive environments.
Geopolymer concrete have been in use in the British ready mixed concrete sector for some time. The last two years saw the introduction of a number of geopolymer and ultra-low carbon precast products into the British and European markets. Earlier this year, in a Europe first, 1.6m diameter ultra-low carbon concrete jacking pipes from Bessac (a subsidiary of Soletanche Bachy) were used in a tunnelling project in France. It is understood that several other concrete pipe manufacturers in the UK, Norway and France are exploring other ultra-low carbon solutions similar to the ones being introduced at FP McCann and Bessac.
FP McCann trials are part of a wider low carbon initiative which will see low carbon solutions being widely utilised and combined with modern manufacturing methods to provide a truly innovative solution for the concrete sector.
FP McCann concrete pipes offer cost and carbon effective solution to M42 link road project
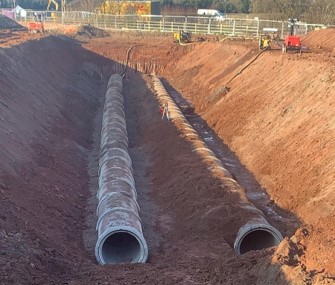
The road link, at junction 6 of the M42 near Solihull, is part of a main £143M contract with Highways England being delivered by Skanska. The project, which started in 2021, is expected to significantly reduce traffic congestion at peak hours.
The diverted mains water were being installed at significantly deep depths, 6 metres under the new road, requiring protection. Severn Trent and their strategic alliance partners Amey employed the services of specialist utilities civil engineering contractors G&V Gallagher to carry out the job. The team decided to employ concrete pipes as a protective sleeve for the mains water pipes being diverted. The DN1200 concrete pipes, procured via builder merchants Wolseley and supplied from FP McCann’s Ellistown factory in Leicestershire, were the obvious choice due their resilience and ability to withstand significant loads, compared to lightweight alternatives. Two 70 metres long runs of concrete pipes were installed. The backfilling for the DN1200 pipeline used “as dug” material and a “Class B” bedding, a type of bedding which can achieve up to 50% savings in granular materials, leading to significant carbon savings compared to the full surround Class S bedding.
G&V Gallagher director Vivian Gallagher noted that they chose FP McCann’s large diameter 1200mm pipes “… as the inherent strength and below ground loading capabilities of reinforced precast concrete gives them a distant advantage over large diameter plastic pipe alternatives”.
British Precast Drainage Association (BPDA) joins the Mineral Product Association (MPA)
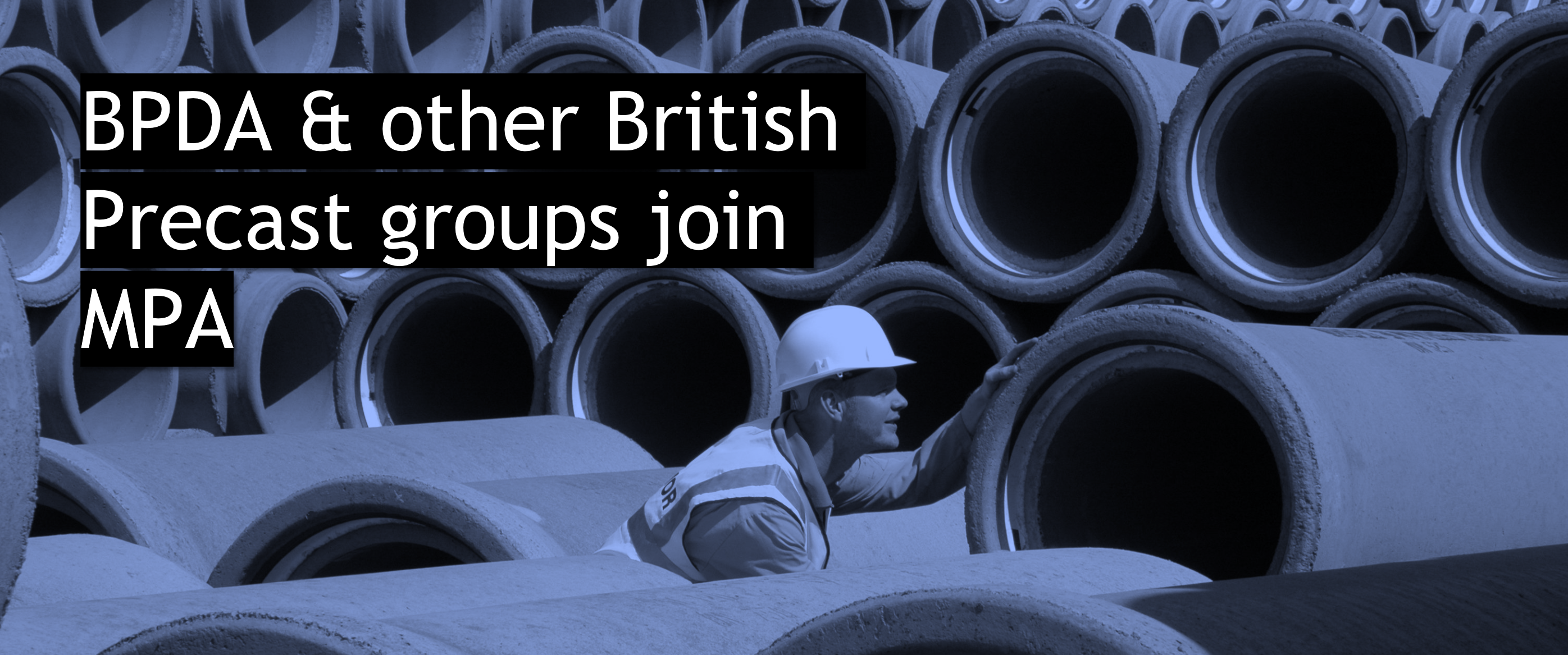
As of 1st January 2022, the British Precast Drainage Association (BPDA), along with the Precast Flooring Federation (PFF), British Precast Architectural & Structural (BPAS) and Interpave, have now become MPA Precast.
Britain concrete producers are joining their forces in one association to represent the industry and accelerate its journey to beyond Net Zero carbon.
British Precast, whose members include manufacturers of concrete masonry, paving slabs, structural sections and drainage systems, has merged with the Mineral Products Association (MPA) which represents all the UK’s cement makers, over 90% of aggregates producers and more than 70% of ready-mixed concrete suppliers.
As of 1st January 2022, two new MPA product groups have been formed as a result of the merger to replace British Precast, MPA Precast and MPA Masonry. The British Precast Drainage Association (BPDA), along with the Precast Flooring Federation (PFF), British Precast Architectural & Structural (BPAS) and Interpave, have now been integrated under MPA Precast.
The merger gives the British concrete industry a single voice, with the sector’s advocacy vehicle – UK Concrete – driving forward a common agenda to set the record straight about concrete’s role in sustainable construction and address the challenges of climate change. The UK concrete and cement industry has already reduced absolute carbon emissions by 53% since 1990 – faster than any other sector of the economy – and the merger will unite the sector behind its ambitious ‘Roadmap to Beyond Net Zero’ by 2050.
Nigel Jackson CEO of Mineral Products Association said: “This is a landmark moment in the evolution of the UK concrete industry which is already a global leader in terms of decarbonisation, recycling and biodiversity enhancement. Now more than ever the concrete industry must work hand-in-glove to promote the essential role this amazing and under-appreciated material plays in our economy and our quality of life. Mitigating the industry’s environmental impacts whilst delivering solutions that help people to adapt to climate change is an important balance to be struck. With the entire sector united and pulling in the same direction we are better able to achieve our shared goals.”
Alan Smith, who retires as President of British Precast, said: “British Precast has been affiliated with the Mineral Products Association for the past decade and the successful relationship we have built has given our members the confidence to fully support this merger. Coming together enables the industry to operate more strategically, rejuvenating our determination to rise to the challenges of climate change and emphasise the importance of our industry in climate adaptation.”
Five facts that make the carbon footprint of concrete attenuation tanks lower than Geocellular alternatives
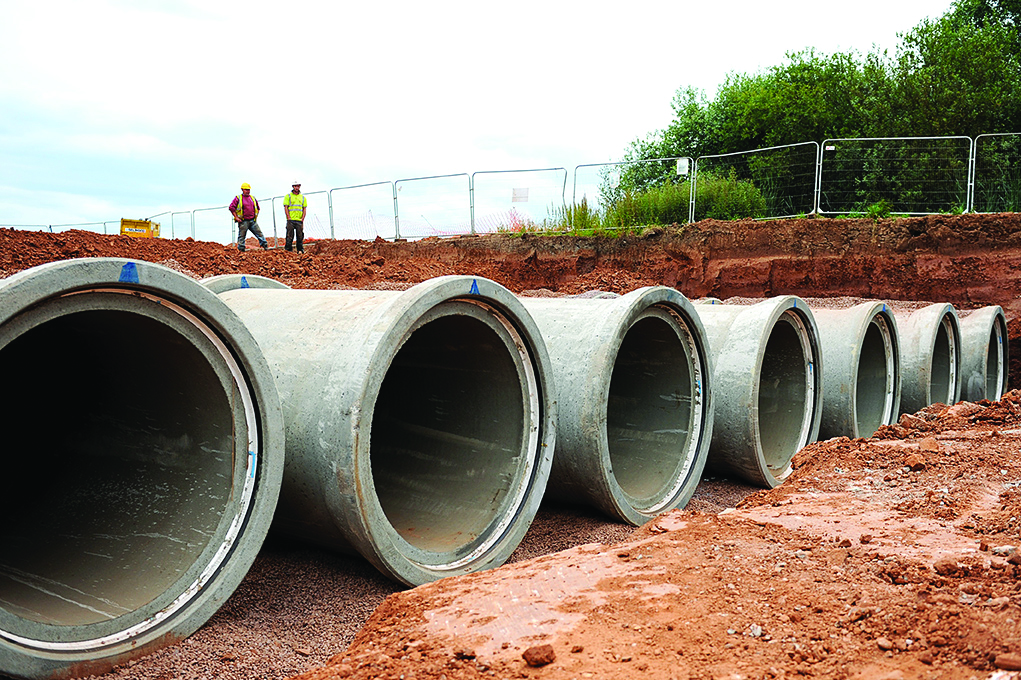
In this blog, we highlight five elements that make all the difference in such underground tank comparisons:
1. Getting the numbers right
Getting the right calculation methodology is crucial. In Whole-life Carbon Assessments there is need for a robust methodology with sound scenarios for each option. Sourcing of right data is also important: The ICE Database is recognised by many in the construction industry as one of the most credible sources of construction-related carbon footprint data. But we need to bear in mind that carbon footprints change constantly and should be subject to continuous checking and scrutiny. This study uses the ICE Database (v.3) numbers as that version is still very recent. Using very simple math:
The concrete pipe tank's mass is around 22 times heavier than an equivalent Geocellular tank. But the carbon footprint of a tonne of mould-injected polypropylene, the material used in that specific type of crate tank, is almost 31 times higher than the carbon footprint of a tonne of concrete pipe. We also ensured that realistic assumptions were developed for products' transport to site, construction on site and End-of-Life. In a few years' time there will be a need for more up-to-date data, and this can only be achieved using recent and valid construction products' Environmental Product Declarations (EPDs) such as this one from the BPDA.
2. Functional Unit & Durability
Bear in mind that the comparison is not simply between two tanks. It is mainly between the services offered by these two tanks: which is the storage and attenuation of a certain amount of stormwater (300 m3) over a specific period of time (+100 years).
If the storage capacity deteriorates over time due to the accumulation of silt, then this needs to reflect on numbers. If a tank has a design life of 50 or 60 years only, then at least one replacement will need to be accounted for (as described in EN 15978) to fulfil the requirement of a +100 years' service life.
3. Use realistic "Transport to Site" and "site installation" scenarios
Development of scenarios for different lifecycle stages is one of the most challenging aspects in Whole Life carbon assessments as any inaccuracies in assumptions can lead to significant over or under-estimation of carbon emissions.
In the transport to site scenarios, instead of using transport factors (such as 0.1065 kg CO2 e/ tonne.km) designed for GHG Protocol calculations, we opted for a different system based on what we know about deliveries and the maximum capacity for trucks used in delivery. Our calculations show that the plastic tank will likely need two deliveries only (at half laden), while the DN2100 concrete pipes will need 12 deliveries at "full laden" truck impact status.
We also avoided the use of any factors for construction activities and carbon emissions. We instead assumed that all plastic tank assembly is manual (carbon free) and calculated the impacts of concrete pipe installation based on the time consumed by a JCB JZ 141 excavator (around 11½ hours excluding idle-time and break-time). The time for excavation and backfilling was assumed to be similar for both systems.
4. Concrete which is unlike any other concrete
A fact often overlooked is that concrete pipes is made of a low carbon type of cement. The cement blend used with concrete pipes, CEM II B-V, uses a 30-35% fly ash content. Over the last few years, we also saw a rise in the use of CEM III blends (which includes GGBS). According to the ICE Database, the carbon footprint of one tonne concrete pipe is around 146 kg CO2 e/t. This number is dropping every year and is likely to reach around 133.4 kg CO2 e/t later this year. Moreover, the carbon footprint of a concrete pipe reaches its peak at the factory gate and then continues to drop every year due to carbonation. Concrete absorbs CO2 through a chemical process associated with the CaO content within its mix. Based on our 3rd party verified EPD, up to 7% of the carbon footprint is likely to be negated by carbonation and the absorption of atmospheric CO2.
In the next 10 years we will see a significant drop in that carbon footprint as more cement manufacturers invest in Carbon Capture & Storage (CCS) and fuel switching technologies. The significant drop in the electricity grid carbon intensity is also likely to have a significant impact on UK concrete pipe factories in the next 10 years which is likely to become very evident.
5. Don't forget the End-of-Life stage
We tend to focus a lot on upfront carbon and forget about the fate of a pipeline at the End-of-Life. At the End-of-Life, a sewerage or drainage pipeline will need to be decommissioned and either exhumed or filled with foam concrete with a very lean mix. In urban areas where the pipes are partially or fully removed, removed concrete pipes can be reused again or crushed and reused as Recycled Concrete Aggregates (RCA). Crushed concrete can absorb vast amounts of CO2, significantly reducing the overall Cradle-to-Grave carbon footprint. The removed plastic crates are either incinerated, releasing anything between 1,000 to 1,500 kg of CO2 per tonne of polypropylene, or recycled and reused in a lower applications.